
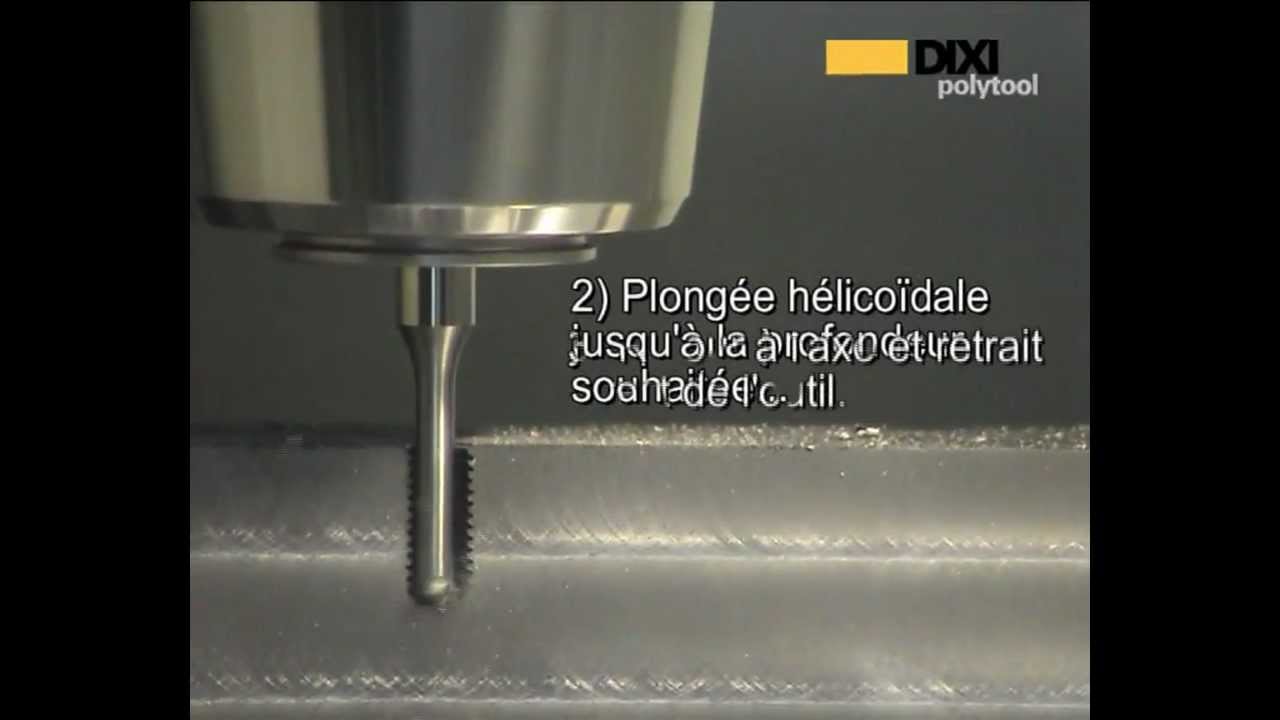
The second focus is on the thermal stability of the entire machine. It starts with the machine bed, which is made of mineral casting, because this material is characterized by a very low thermal reaction and dampens the high-frequency vibrations occurring during machining up to 10 times better than steel. This approach includes all essential components of the system - from the base frame to the control system, the axis drives and the spindle to the milling tools.

"This can only be achieved if the entire machining process is thoroughly optimized," reveals K.-H.
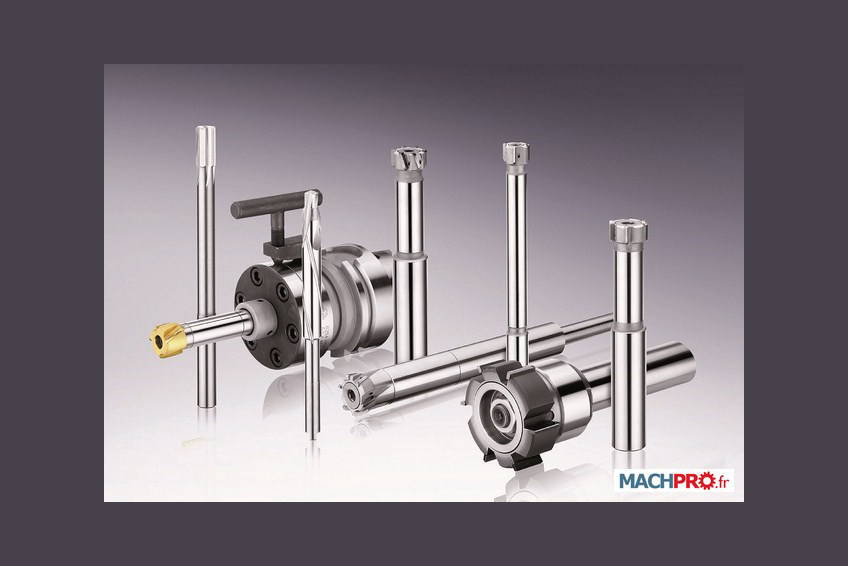
The accuracy requirements for the milling machines used to manufacture the tools are correspondingly strict. Tolerance specifications in the µm range are therefore common practice today. For mold and tool making, this naturally means that the molds and tools required for production must be manufactured more accurately by around one order of magnitude. Whereas previously tenths of a millimeter had to be adhered to, today hundredths need to be met. The rapid spread of zero-error philosophies means that the tolerance specifications have been getting stricter.
Dixi polytool usa drivers#
The drivers for this are ever higher demands on quality, reliability and service life. This applies to almost all products, from simple sheet metal stampings to sophisticated injection or die cast parts. "In virtually all industrial sectors, the requirements placed on component accuracy are constantly increasing," explains K.-H. Glunk. Gallery with 9 images Increasing Demands on Precision
